针对煤层气(天然气)发电排放的500℃高温烟气,复旦大学先进材料实验室主任、中国科学院院士赵东元教授领导的研究团队与太阳成集团范建伟副教授团队合作,成功研发了适用于500℃高温烟气脱硝的催化剂,并完成了现场中试实验,脱硝效率稳定大于95%,该成果在煤层气、天然气发电烟气及窑炉烟气的脱硝领域具有广阔的市场前景,并突破了国外技术在烟气脱硝领域的技术垄断。
该团队研发的低温(200°C)脱硝催化剂及系列化成套脱硝装备曾获中国市场协会金桥奖、上海市科技进步三等奖等奖项,被广泛应用于不锈钢酸洗、湿法冶炼、催化剂制备、化工制造等行业的烟气脱硝。
煤层气或天然气发电厂尾气中含有CH4、NOx等排入大气后,通过物理及化学作用,引发酸雨、光化学烟雾和臭氧层空洞等环境问题,对环境、人类健康和生产活动均有较大的危害,已引起了世界各国的普遍重视。
最有效的脱硝方法为SCR(selective catalytic reduction),其中最核心的是催化剂的设计和选用。煤层气(天然气)发电尾气中含有600-700 mg/m3左右的NOx及30 mg/m3以下的SOx。根据最新的环保法规要求,NOx需减排至120 mg/m3以下。
燃煤电厂烟气脱硝催化剂的制备(320-380℃)的核心技术由外国企业长期垄断。而煤层气或天然气发电的余热温度为500℃左右,以往的技术已经无法满足,如果选用燃煤电厂中大规模使用的V/Ti系列脱硝催化剂,由于其最佳反应温度为320 ~ 380 °C之间,则必须改造烟气余热利用系统,同时将此烟气进行反复换热后进行常规的脱硝处理。
研发直接应用于500 °C工况下的脱硝催化剂,对煤层气发电系统影响最小,并可以大幅度降低投资,运营管理也更加方便,具有非常重要的现实意义。同时,在煤层气发电尾气脱硝处理领域也具有推广意义。
复旦大学先进材料实验室主任、中国科学院院士赵东元教授领导的研究团队与太阳成集团范建伟副教授团队合作,采用先进功能纳米材料制备工艺,利用纳米自组装技术制备了介孔沸石分子筛材料作为催化剂载体,利用固相纳米浇铸(Nanocasting)和原位生成技术将活性组分组装到介孔沸石分子筛的孔道中,制备了脱硝催化剂,开发出了适合煤层气发电高温烟气(500 °C)的脱硝催化剂。上海同济科蓝环保设备工程有限公司利用此项具有自主知识产权的科研成果,规模化生产了高温脱硝催化剂,并应用于晋煤集团煤层气发电余热尾气的中试试验,取得了优异的脱硝效果。现场中试实验,脱硝效率稳定大于95%。
该成果在煤层气、天然气发电烟气及窑炉烟气的脱硝领域具有广阔的市场前景。该团队研发的低温(200°C)脱硝催化剂及系列化成套脱硝装备曾获中国市场协会金桥奖、上海市科技进步三等奖等奖项,被广泛应用于不锈钢酸洗、湿法冶炼、催化剂制备、化工制造等行业的烟气脱硝。
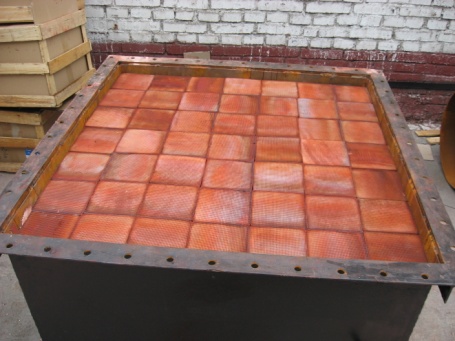
催化剂组件
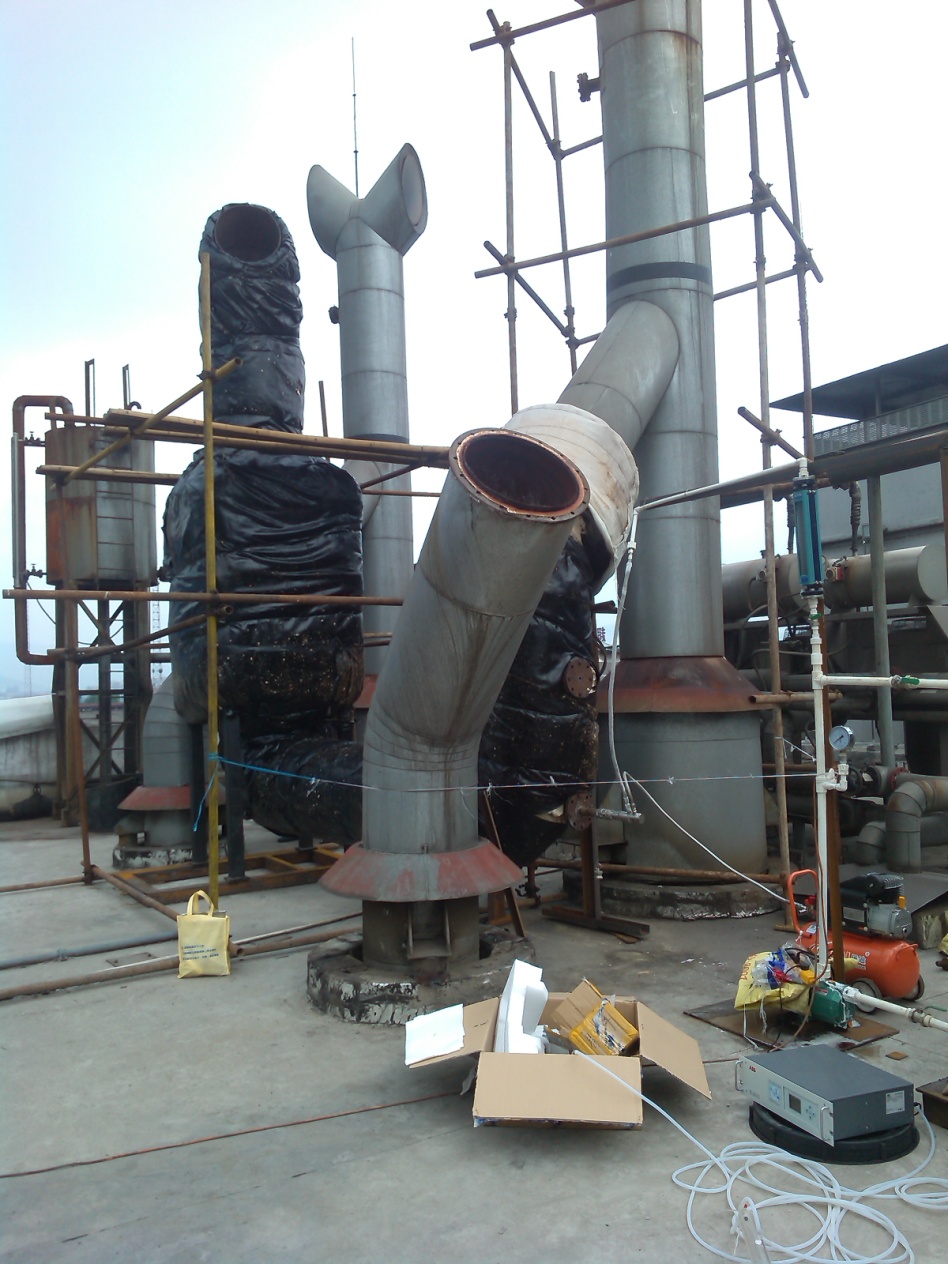
中试现场
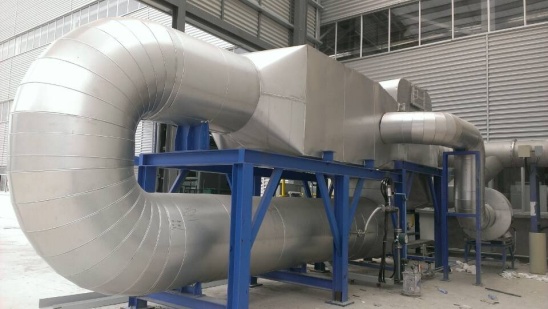
成套装备